Inspections
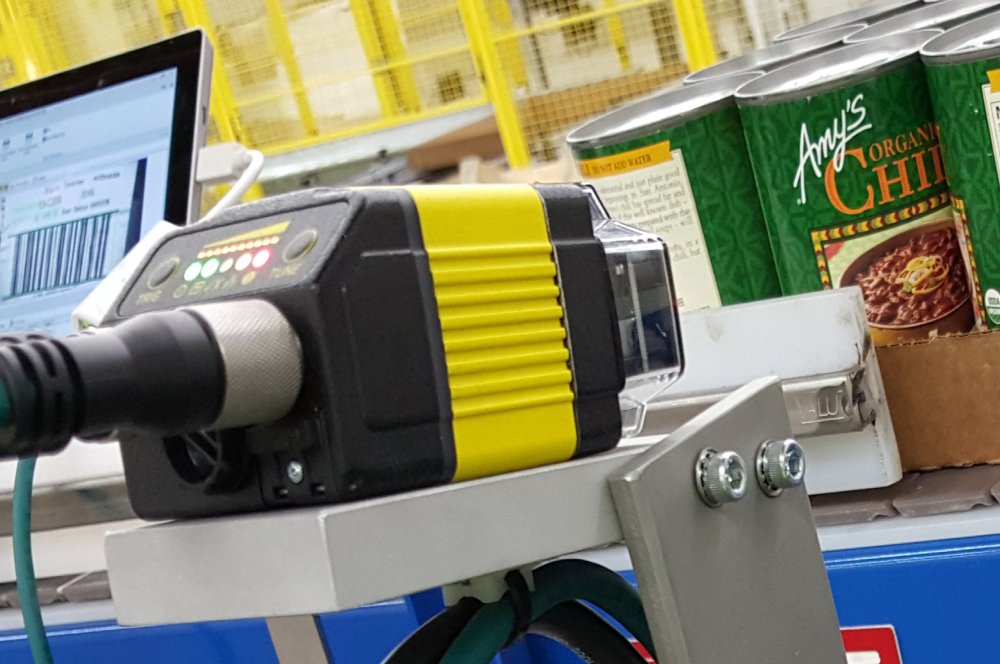
Barcode verification(Optional)
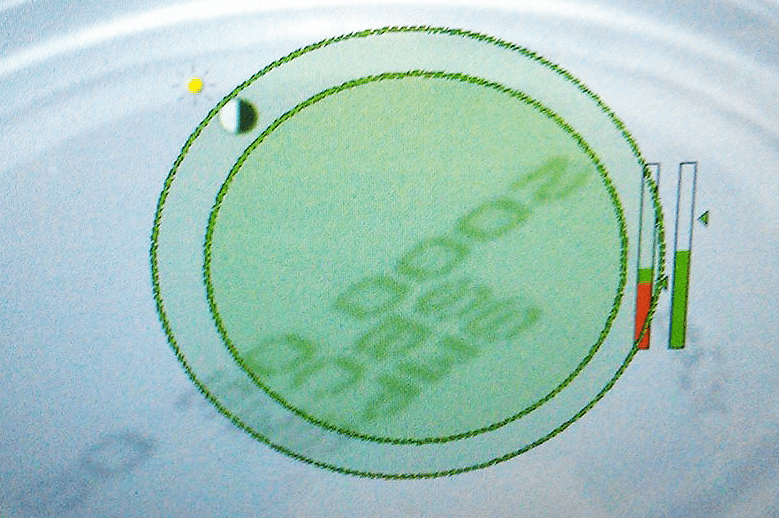
Presence of label
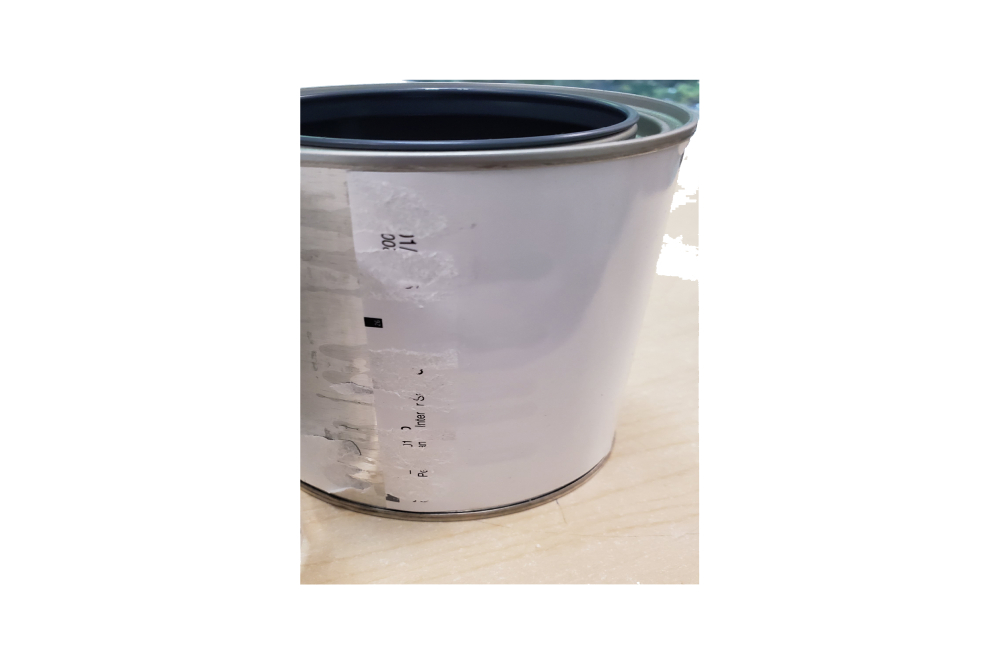
Proper glue application
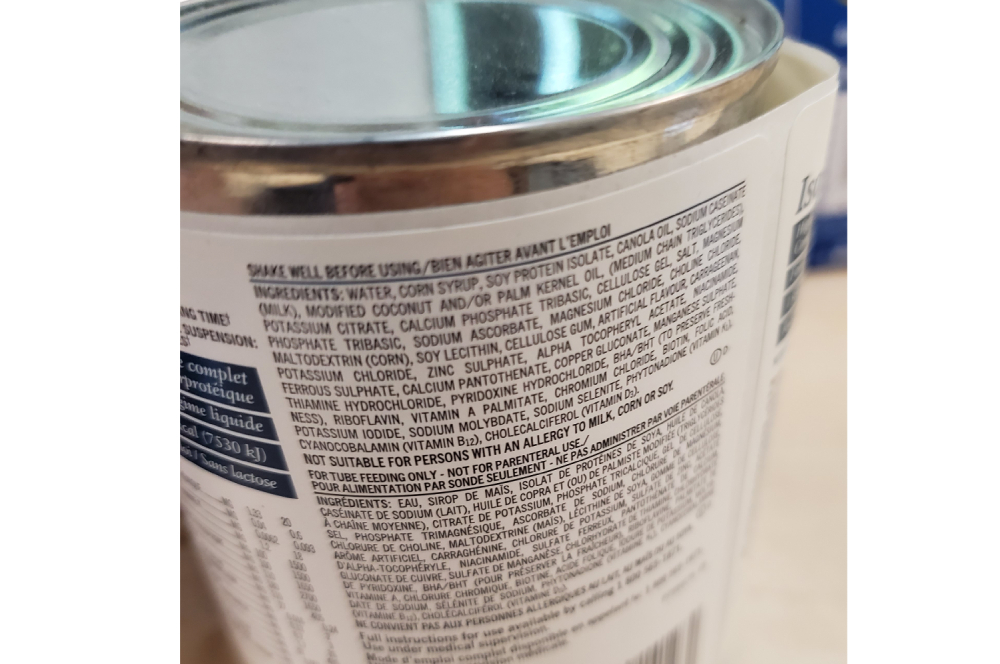
Loose labels

Dog-eared labels
Technology
The RTLI brings an innovative approach to label inspection. The RTLI is designed to smoothly integrate into a line immediately after a roll through labeler. As the can rolls through the inspection area, it is tested for the presence of a label (shiner), improper glue application (flapper) and loose labels. Bar code verification is available through optional add-on module. The bar code module insures that the correct label is applied to the can.
This machine can also be complimented by a Variety Code inspection system (Can Code OCV) that verifies the inkjet printer code on the end of the can and matches it to data read by the barcode reader. Using both the barcode reader and the Can Code OCV verifies that the label matches the product in the can, virtually eliminating the possibility of incorrect labels being applied. If defects exist, the can is ejected from the line by one of two methods. First method is two eject after it is stood up after a can twist and the second is by an integrated progressing door eject system.
Features
- The RTLI contains visual feedback from camera based sensors for easy changeovers and setup.
- Touch display Human Machine Interface (HMI)
- 100% inline inspection of every can.
- Quick and easy changeovers with one touch training
- Intuitive setup commands that are easy to use
- Precision sensor adjustments for accurate inspections and fast changeover times
- Inspects large variety of can types and sizes
- Highly reliable electrical design in even the most harsh and noisy environments
- Attaches to discharge of all Roll through la
Specifications
Specifications | |
---|---|
Operating Speed | 1200 Inspections per min max |
Power Requirements | 100-250 VAC isolated incoming power |
Pneumatic Requirements | 45-65 psi; ¼” standard (Options available) |
Spacing Requirements | Zero backline pressure from containers. Accumulation should stop 20 inches from discharge |
Display | LCD Color touch display for general control and separate for barcode reader output. |
Operating Conditions | Stable Ambient Temperature: 32º to 122º F (0º - 50º C) |
Communications | Standard line control discrete I/O Extended I/O available for results, status and line control |
Enclosure | Nema 12 std (Nema 4, IP 65 optional ) |
Length | 54.0” Standard; |
Eject | Stand-up eject after twist off single lane conveyor or Progressing trap door eject. Stand-up eject can be paired with eject table with sensors to verify eject (optional). |
Interface | Intuitive with multiple access levels |
Construction | Stainless Steel, engineered plastics and anodized aluminium (Durable construction for the food and beverage industries) |